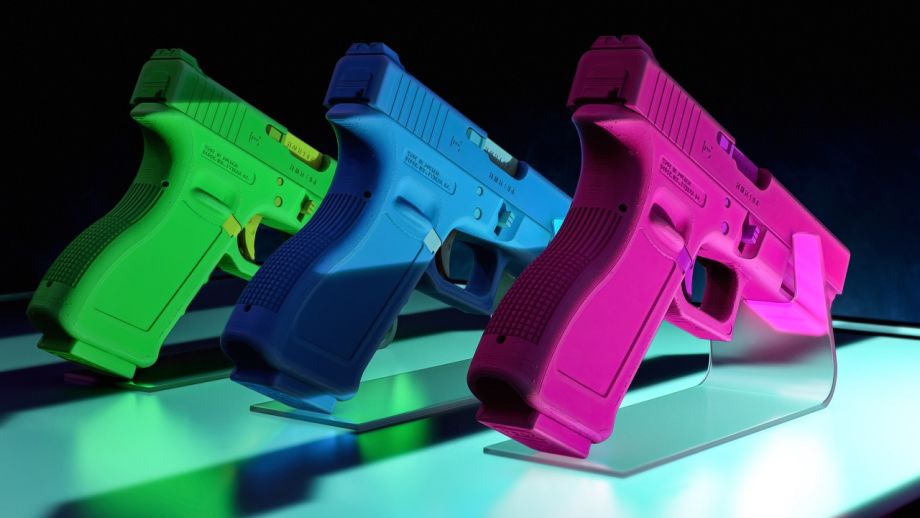
Recently, I was looking for a method to recreate 3D printing and CNC patterns directly on 3D models. After some trials and errors, I found a way that makes your model look like it was really manufactured by these tools. There are 3 key software packages we need to use to achieve this effect: Fusion 360, Voxelizer, and ZBrush to optimize, polish, decimate, and set everything together. In the current example, I’m going to use my Glock 17 that I made directly in Fusion 360, you can download it for free.
Getting Started
With the help of Fusion 360, it is possible to physically simulate 3D printing and CNC milling effects directly on your model. To improve the realistic effect and add more details, we need to generate the so-called G-Code from a 3D printing simulation. A G-Code file is a set of specific instructions for a 3D printer to print your model. Keep in mind that by rotating your model to make it face the printer extractor, you may achieve totally different patterns.
First, let's setup a 3D printer. You need to import your model into Fusion 360 or model it directly in this package. It’s also possible to skip the Fusion 360 steps and use Voxelizer directly to generate G-Code instead, but you are going to miss many additional options and flexibility. Simulation is going to reflect your 3D printer settings and printer manufacturer parameters.
Select the workspace drop-down menu and choose the MANUFACTURE tab to change your working space.
In the manufacture workspace, select the ADDITIVE tab to access a 3D printing setup and click SETUP.
Proceed to the Fusion 360 library and select the printer your model should be simulated with, in this case, I used Alfawise U20. In the FILTERS tab, you can filter printers by the printing tech they utilize such as FFF, SLS, SLA, etc. In our case, we need the FFF technique to simulate the Additive Toolpath.
The next step is to select filament size. The best pattern could be achieved by selecting between ABS 1.75 mm or ABS 2.85 mm. In the printer settings editor LAYER HEIGHT represents how big your steps are going to be, you may keep it as a standard setting or change it to something between 0.15-0.2 or if you prefer a bigger stairs effect, increase this number. FILAMENT DIAMETER is your filament thickness, so increasing this size can give you a different pattern effect. You can access all these options later by clicking the right mouse button on filament ABS 1.75 in our case, and press EDIT).
The Extrusion tab affects the inner thickness areas of the 3D print.
The parameter that we need to look at here for is INFILL EXTRUSION WIDTH, that’s how you could adjust how thick your line is going to be.
Here are some examples of how it affects the simulation end result. On the first screen, our setting is 1.4, and 0.4 is on the second.
The Shell tab affects your inner pattern.
Here we can change the NUMBER OF PERIMETERS value, that’s going to affect how many inner offset shells will be produced to cover holes in the extruder movement direction. Another important parameter is the TOP AND BOTTOM INFILL ANGLE. This one affects which pattern is going to be used to close holes in the extruder direction. If your number is 0 then the 3D printer won’t be making a zigzag pattern and use just perimeters offset to cover top areas.
For example, here are two different settings on these screenshots. On the first one, the infill angle is set to 0 and perimeters to 20. On the second, perimeters are set to 0, and the infill angle is set to 45.
Number of perimeters 20, top and bottom infill angle 0
Number of perimeters 0, top and bottom infill angle 45
The Infill tab affects the pattern inner support layer.
INFILL DENSITY responds for pattern tiling value and INFILL PATTERN for which pattern is going to be used as a support. INFILL ANGLE affects your support pattern angle. It’s possible to simulate inner support too in general but it will increase processing time and polycount, which is not worth it in my opinion.
The Lattice Add-On
I recommend using the Lattice add-on for Fusion 360, which can be accessed through the DESIGN tab. Here’s a video on how to install this addon.
To convert your Fusion 360 body into a lattice object, access VOLUMETRIC LATTICE from the MODIFY tab in the DESIGN workspace
The next step is to change the settings of your lattice and thickness.
The SETUP tab is responsible for general settings, and the SOLIDITY tab affects your lattice thickness. After you are done setting up your lattice, it’s time to convert it to something solid.
Click on the body you just applied your lattice to with the right mouse button and select CREATE MESH from the VOLUMETRIC LATTICE ACTIONS drop-down menu.
Right-click on your newly created mesh object and save it with SAVE AS MESH using the STL format. You can directly import STL files into ZBrush, just don’t forget to use DISPLAY PROPERTIES – FLIP to turn your mesh. Use INFLATE and LIVE BOOLEANS to create a slice effect and reveal your inner support lattice.
Print Bed Adhesion controls your initial layer during the printing process.
I recommend unchecking the checkbox atop to remove it from the simulation process. Otherwise, you need to remove it in the ZBrush polishing stage. If this is what you are looking for, just leave all settings as they are.
The Support tab affects the printing support tree for your model during the printing process.
If you are looking to make a support tree as a part of your model, set the NUMBER OF SUPPORT PERIMETERS to 1 or more, otherwise set it to 0. However, to have more control over your support, it’s better to create supports separately from the MANUFACTURE tab. It’s also possible to generate supports directly in Voxelizer. I find it’s easier and faster to use Voxelizer to generate supports, also, you have more support options, however, you are going to sacrifice some Fusion 360 flexibility.
At the end of your simulation setup, it’s recommended to change your post process name, it will affect your file name in the end and is going to help to manage your project too. This parameter can be accessed by right-clicking on your simulation setup.
You should also align your model to the 3D printing area. Fusion 360 is going to show areas of your model that are not in the printer area and will be ignored. If your model is completely outside of the printer area, it will show an error.
Now, it’s time to simulate our 3D printing process.
Right-click on your Additive Toolpath and select SIMULATE ADDITIVE TOOLPATH.
In the next window, click CALCULATE and wait until your simulation is complete.
By using the arrow in the center of your model, you can see the 3D printed simulation layer by layer or you can press the play button as well as the end result in the animation controls.
When you are satisfied with your final simulation, press POST PROCESS in the SIMULATE ADDITIVE TOOLPATH window or right-click in the left outliner.
This tab is going to allow us to save the 3D printer path and our parameters as G-Code, which we can use in Voxelizer to recreate our model from voxelization.
Voxelizer
Voxelizer is free software you could use for your 3D printer setup and adjustments. You can download this software from the official website. Download Voxelizer for FAB, this’s the latest version that we are going to use to generate our model from G-Code.
Voxelizer has a really simple and user-friendly interface. To import the G-Code file, simply press on the box in the middle of the screen or press FILE – IMPORT – G-CODE.
After we imported our model into Voxelizer, we should open the DIAGNOSTIC tab and press ENGAGE VOXEL SIMULATION.
The best settings for the voxel size that I found are around 0.085-0.09, increasing this value higher will produce a more blurry result but it will take less time to process.
When we press "okay", a new window with different options is going to appear. Be patient, this process can take from 30 minutes to 1 hour, but trust me, it’s processing. Unfortunately, during this time, there will be no progress bar, and once it’s finished, your model is going to appear in the viewport.
If your simulation is taking too long, try to increase the voxel size or use VOXELIZE or VOXELIZE PRECISE instead of DIAGNOSTIC SIMULATION.
When the process is complete, you will start seeing your model in the viewport. Click on your model or go to the TREE STRUCTURE tab and select PRINT SIMULATION. Then press FILE – EXPORT – STL and save your STL.
Now you can import your model into ZBrush, clean it, DynaMesh (if necessary), use DEFORMATION – CONTRAST to add extra sharpness, and export it after using the DECIMATION MASTER.
CNC
This process is quite similar to the 3D printing process except that we need to use the MILLING tab this time.
Instead of selecting a 3D printer, we need to select a milling machine and correct the milling tool.
Different settings are going to give you different results.
Milling machines use different axis and different milling movements, each of them needs to be set separately from one another, however, in the end, if you are going to simulate the whole milling project, Fusion 360 is going to apply all operations at once on your model. In this specific example, let’s start with the PARALLEL milling option.
It’s very important to uncheck CONTACT ONLY, as well as to change TOOL CONTAINMENT to TOOL OUTSIDE BOUNDARY in the GEOMETRY tab so the milling tool could access different areas of your model.
When everything is ready, you may proceed to the simulation process by right-clicking on your milling project in the outliner.
After your simulation is complete, right-click on it and press SAVE STOCK, save it as an STL file. One more thing you should keep in mind: your simulation timeline is going to affect your saved STL file too. So, if you want to export just a partially milled object, move your time accordingly and save it from this specific time frame.
Serge Karpovs, 3D Artist
Keep reading
You may find these articles interesting